Hooked on Agriculture Technology
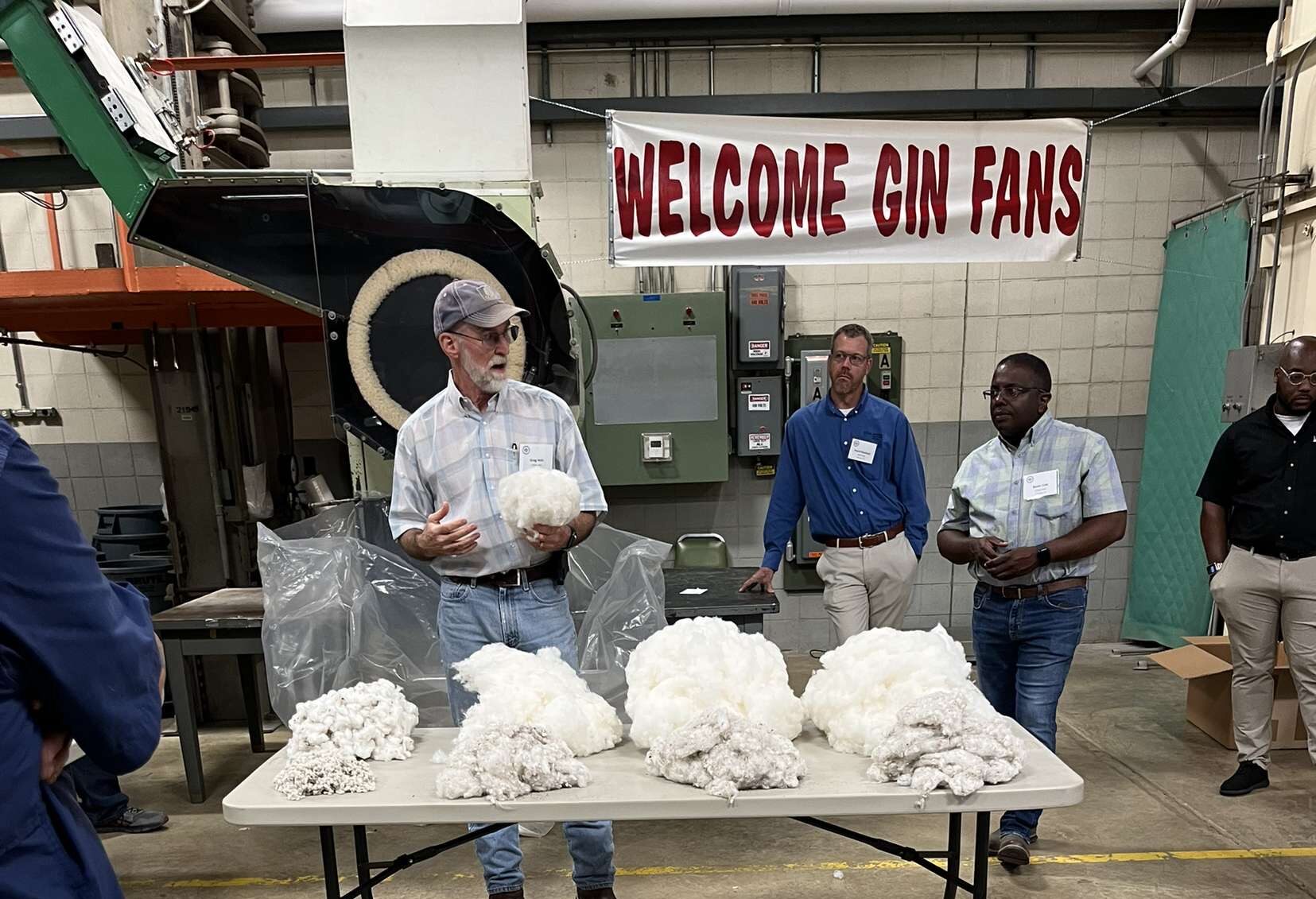
By Laura Riddle
Some people were born to be rock stars. Wayne County, North Carolina native Max Hooks not only looks like he belongs on center stage, but he has the credentials to back it up too.

As an undergraduate in the Department of Biological and Agricultural Engineering, Hooks assisted BAE Extension Associate Professor Grant Ellington on a tobacco research project and was a Teaching Assistant for three of BAE Lecturer Tommy Stephenson’s courses. He was also a member of the 2022 Pack Pullers and currently serves as a team advisor.
Now a BAE alumnus and third-generation NC State graduate, he is on the path to completing a master’s in biological and agricultural engineering.
Postharvest Cotton
“My research involves improving efficiency and preserving the quality of cotton fiber during postharvest processing by developing a device to assess seed cotton moisture levels prior to ginning,” Hooks says about the project sponsored by Cotton Incorporated.
Cotton modules have been around for decades, gradually improving supply chain delays and yield quality between harvest and ginning. The most recent advancements made machines commercially available that could both pick and form modules.
The challenge commercial gins are facing now is the time-consuming process of assessing modules with varying levels of moisture prior to ginning and the amount of energy used for the ginning system to adjust between each module.
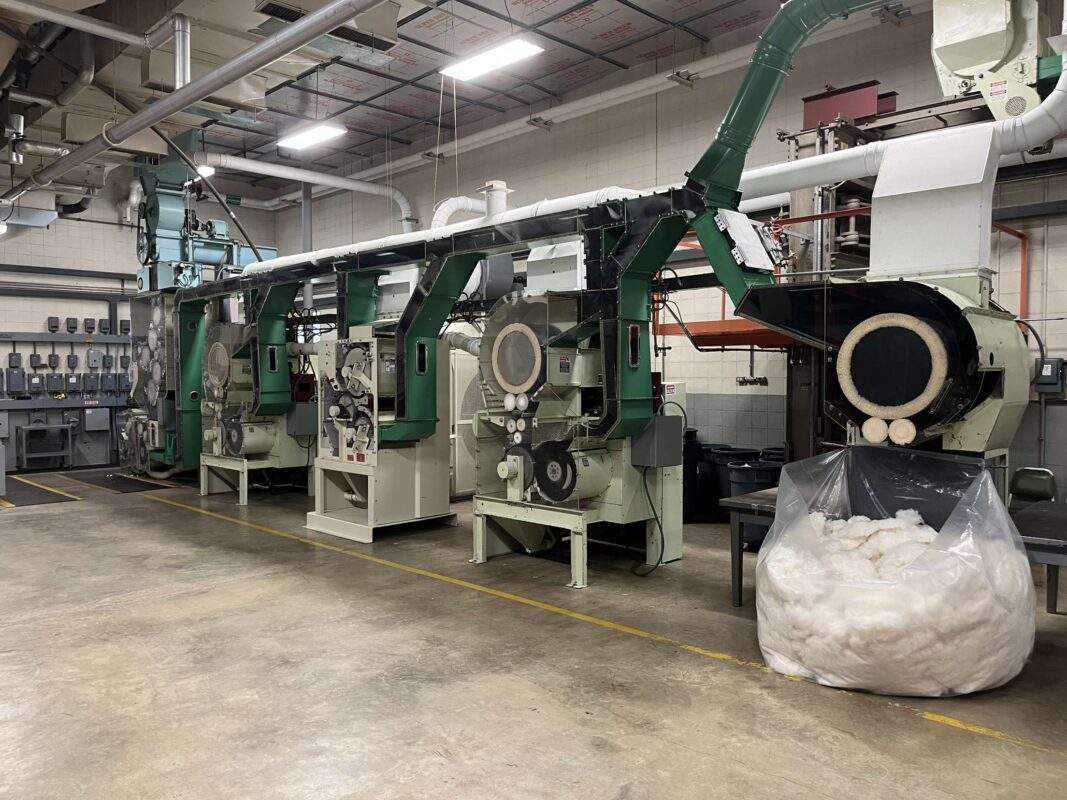
“The objective is for the device to sense moisture levels within the module while the front-end loader is moving it around,” Hooks explains. “This removes the need for one person to individually test each module because they’ll be able to get a real-time measurement as soon as they pull a module off of the truck at the gin. Also, they can begin staging modules by moisture levels to reduce the time and energy needed for the system to accommodate those moisture variations.”
Earlier this year, Hooks attended the Beltwide Cotton Conference in New Orleans where he first heard about the National Cotton Ginners Association Gin School and Ginner Certification. Upon looking into the program and the different certification levels, Hooks saw an opportunity to gain insights that could further impact his research.
“Participating in Gin School roots Max’s project in the day-to-day experiences of ginners and reinforces why sensing cotton module condition prior to ginning is important,” says Hooks’ advisor and BAE Assistant Professor Jason Ward. “Connecting research to its stakeholders is essential and the best way to learn is by getting side by side with the people who do the work every day.”
Back to School
“I’d been gathering some background knowledge on what affects fiber quality,” Hooks says, “and so I thought if I can actually see what those processes are, I can more accurately create a system that’s going to analyze the right things.”
Gin certification is offered at three levels, with each level advancing on the previous course training. The Level 1, three-day course covers topics ranging from basic gin safety to cotton classification and moisture measurement. In June, Max, along with Ward, attended the Stoneville Ginners School located at the USDA Ginning Research Laboratory in Stoneville, Mississippi.
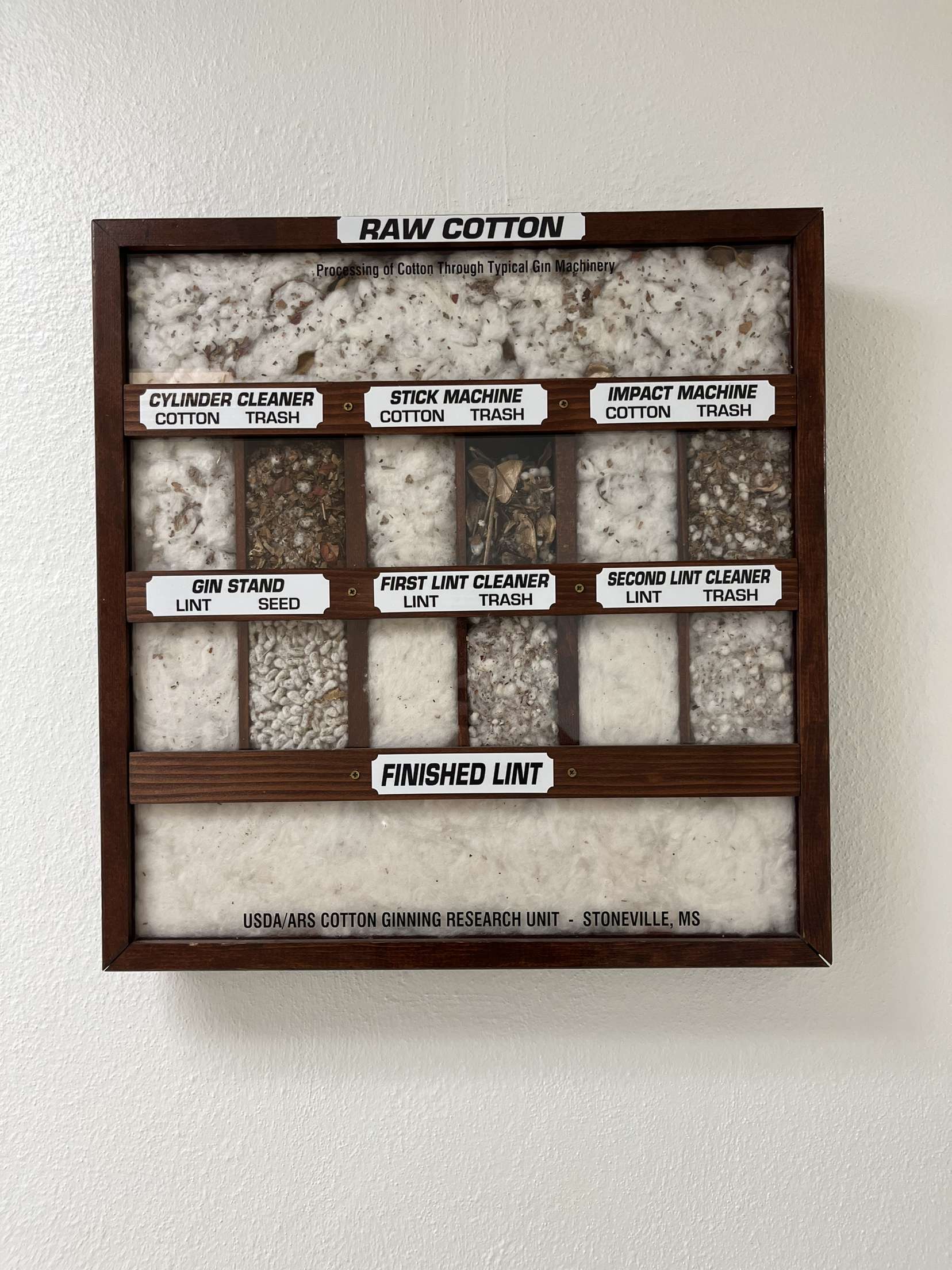
Hooks and Ward were also invited to visit the USDA Cotton Classing Office in Memphis, Tennesse by NC State alumnus and Texas A&M Biological and Agricultural Engineering Assistant Professor Robert Hardin. They were able to see the assembly of cotton classing boxes, which are shared annually with other countries as the international standard for grading cotton.
“What I learned was not only what each component of the gin is, but also what each component of the gin does and how it affects fiber quality,” he says.
The experience benefits Hooks in a base knowledge moving forward in his research. “I know that doing something between harvest and ginning to fill some gaps that have not previously been investigated could very well help increase the efficiency and decrease the energy usage of the gin.”
- Categories: